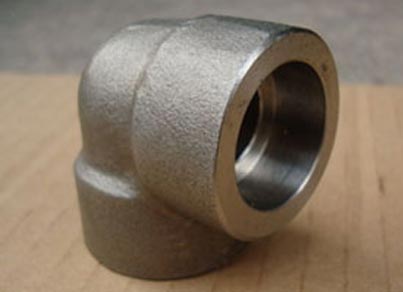
Elbows
Forged fitting elbows are crucial components in piping systems, designed to change the direction of flow. Made from high-quality forged steel, these elbows offer superior strength, durability, and resistance to high pressures and temperatures. Commonly available in 45-degree and 90-degree angles, forged elbows provide a tight radius for optimal flow characteristics.
They are used in various industries, including oil and gas, chemical processing, and power generation, where reliability is essential. The forging process enhances the material's mechanical properties, ensuring that these fittings can withstand the stresses of demanding applications while providing a secure, leak-proof connection.
Specification | Details |
---|---|
Material Grades | ASTM A105, A350 LF2, A182 F1, F5, F9, F11, F22, F304, F316 |
Standards | ASME B16.11, ASTM A234, MSS-SP-79 |
Sizes | 1/2" to 4" (DN 15 to DN 100) |
Types | Elbow (45°, 90°, 180°) |
Pressure Ratings | Class 3000, Class 6000, Class 9000 |
Connection Type | Threaded or Socket Weld |
Corrosion Resistance | Moderate (depends on material grade; may require protective coatings for enhanced resistance) |
Surface Finish | Black, Galvanized, or as specified by customer |
Testing & Certification | Hydrostatic Testing, Positive Material Identification (PMI), Mill Certificates |
Applications | Oil & Gas, Chemical Processing, Power Generation, Marine, and Construction |
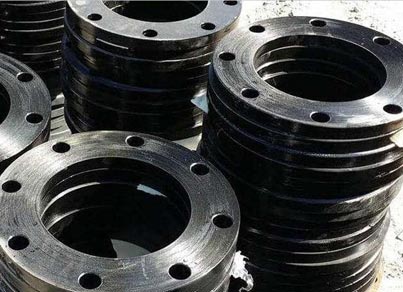
Flanges
Forged fitting flanges are vital components in piping systems, designed to connect two pipes, valves, or other equipment securely. Manufactured from high-quality forged steel, these flanges offer superior strength and durability, making them suitable for high-pressure and high-temperature applications.
They come in various types, including blind, slip-on, threaded, and weld neck flanges, allowing for versatile installation options. Forged flanges are commonly used in industries such as oil and gas, petrochemical, and power generation, where reliability and leak-proof connections are essential. The forging process enhances their mechanical properties, ensuring they can withstand harsh environments and heavy loads, thereby ensuring long-term performance and safety in critical applications.
Specification | Details |
---|---|
Material Grades | ASTM A105, A350 LF2, A182 F1, F5, F9, F11, F22, F304, F316 |
Standards | ASME B16.5, ASME B16.47, MSS-SP-44 |
Sizes | 1/2" to 24" (DN 15 to DN 600) |
Types | Slip-On, Weld Neck, Threaded, Blind, Socket Weld |
Pressure Ratings | Class 150, Class 300, Class 600, Class 900, Class 1500, Class 2500 |
Bolt Hole Patterns | ANSI Standard, with sizes varying by class and diameter |
Corrosion Resistance | Moderate (may require coatings for enhanced corrosion protection) |
Surface Finish | Black, Galvanized, or as per customer specifications |
Testing & Certification | Hydrostatic Testing, Positive Material Identification (PMI), Mill Certificates |
Applications | Oil & Gas, Chemical Processing, Power Generation, Water Treatment, and Construction |
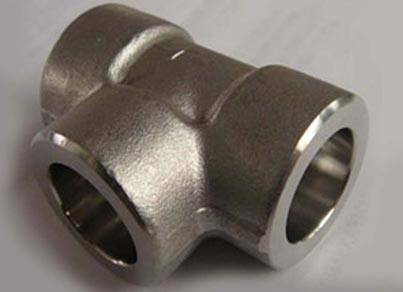
Tee
Forged fitting tees are essential components in piping systems, designed to branch off or combine two flow paths. Made from high-quality forged steel, these tees offer superior strength and durability, making them suitable for high-pressure and high-temperature applications.
Available in various configurations, including equal and reducing tees, they provide a reliable connection point for additional piping. Commonly used in industries such as oil and gas, chemical processing, and power generation, forged tees ensure leak-proof connections and are capable of withstanding harsh environmental conditions. The forging process enhances their mechanical properties, ensuring long-lasting performance and safety in critical applications.
Specification | Details |
---|---|
Material Grades | ASTM A105, A350 LF2, A182 F1, F5, F9, F11, F22, F304, F316 |
Standards | ASME B16.11, MSS-SP-79 |
Sizes | 1/2" to 4" (DN 15 to DN 100) |
Types | Equal Tee, Reducing Tee |
Pressure Ratings | Class 3000, Class 6000, Class 9000 |
Connection Type | Threaded or Socket Weld |
Corrosion Resistance | Moderate (depends on material grade; may require protective coatings for enhanced resistance) |
Surface Finish | Black, Galvanized, or as specified by customer |
Testing & Certification | Hydrostatic Testing, Positive Material Identification (PMI), Mill Certificates |
Applications | Oil & Gas, Chemical Processing, Power Generation, Marine, and Construction |
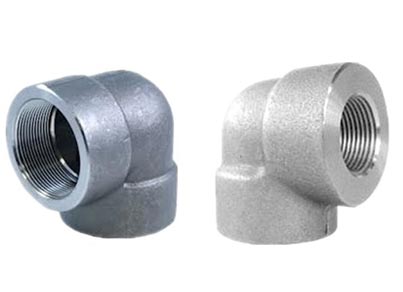
Threaded Elbow
Forged fitting threaded elbows are crucial components in piping systems, designed to change the direction of flow with threaded connections. Made from high-quality forged steel, these elbows provide superior strength and durability, making them suitable for high-pressure applications.
Available in various angles, such as 45-degree and 90-degree, threaded elbows allow for easy installation without the need for welding, making them ideal for situations where disassembly is required. Commonly used in plumbing, oil and gas, and chemical processing industries, they ensure a secure, leak-proof connection while providing flexibility in piping configurations. The forging process enhances their mechanical properties, ensuring they can withstand harsh environments and heavy loads, thus ensuring long-term performance and reliability in critical applications.
Specification | Details |
---|---|
Material Grades | ASTM A105, A350 LF2, A182 F1, F5, F9, F11, F22, F304, F316 |
Standards | ASME B16.11, ASTM A234, MSS-SP-79 |
Sizes | 1/2" to 4" (DN 15 to DN 100) |
Types | 45-Degree Threaded Elbow, 90-Degree Threaded Elbow |
Pressure Ratings | Class 3000, Class 6000, Class 9000 |
Connection Type | Threaded |
Corrosion Resistance | Moderate (depends on material grade; may require protective coatings for enhanced resistance) |
Surface Finish | Black, Galvanized, or as specified by customer |
Testing & Certification | Hydrostatic Testing, Positive Material Identification (PMI), Mill Certificates |
Applications | Plumbing, Oil & Gas, Chemical Processing, Water Treatment, and Construction |
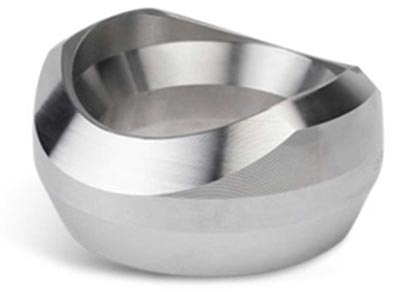
Welding Outlet
Forged fitting welding outlets are essential components in piping systems, designed to facilitate the connection of branch pipes to a main pipeline. Manufactured from high-quality forged steel, these outlets offer superior strength and durability, making them suitable for high-pressure and high-temperature applications.
The welding outlet allows for a secure weld joint, providing a reliable and leak-proof connection. Commonly available in various sizes and configurations, such as threaded or plain, these fittings are widely used in industries like oil and gas, chemical processing, and power generation. The forging process enhances their mechanical properties, ensuring long-lasting performance and safety in critical applications, while also allowing for easy installation and maintenance.
Specification | Details |
---|---|
Material Grades | ASTM A105, A350 LF2, A182 F1, F5, F9, F11, F22, F304, F316 |
Standards | ASME B16.11, MSS-SP-79, ASTM A234 |
Sizes | 1/2" to 4" (DN 15 to DN 100) |
Types | Threaded or Socket Weld Welding Outlet |
Pressure Ratings | Class 3000, Class 6000, Class 9000 |
Connection Type | Welding Outlet (butt weld) |
Corrosion Resistance | Moderate to High (depends on material grade; may require protective coatings for enhanced resistance) |
Surface Finish | Black, Galvanized, or as specified by customer |
Testing & Certification | Hydrostatic Testing, Positive Material Identification (PMI), Mill Certificates |
Applications | Oil & Gas, Chemical Processing, Power Generation, Water Treatment, and Construction |
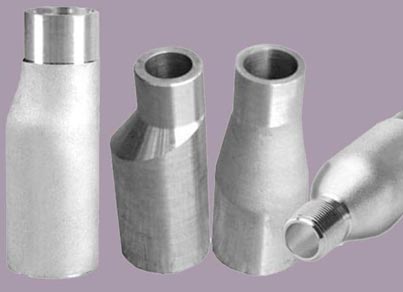
Pipe Swage
Forged fitting pipe swages are specialized components used in piping systems to transition between different pipe sizes or shapes. Made from high-quality forged steel, these swages provide enhanced strength and durability, making them suitable for high-pressure applications.
Designed to connect pipes of varying diameters, swages facilitate smooth flow and reduce turbulence, ensuring optimal system performance. They are commonly used in industries such as oil and gas, chemical processing, and construction, where reliable connections are critical. The forging process enhances their mechanical properties, ensuring they can withstand harsh environments and heavy loads while maintaining a secure and leak-proof seal in piping systems.
Specification | Details |
---|---|
Material Grades | ASTM A105, A350 LF2, A182 F1, F5, F9, F11, F22, F304, F316 |
Standards | ASME B16.11, MSS-SP-79, ASTM A234 |
Sizes | Custom sizes, commonly ranging from 1/2" to 8" (DN 15 to DN 200) with varying diameters |
Types | Concentric Swage, Eccentric Swage |
Pressure Ratings | Class 3000, Class 6000, Class 9000 |
Connection Type | Butt Weld or Socket Weld |
Corrosion Resistance | Moderate to High (depends on material grade; may require protective coatings for enhanced resistance) |
Surface Finish | Black, Galvanized, or as specified by customer |
Testing & Certification | Hydrostatic Testing, Positive Material Identification (PMI), Mill Certificates |
Applications | Oil & Gas, Chemical Processing, Power Generation, Water Treatment, and Construction |
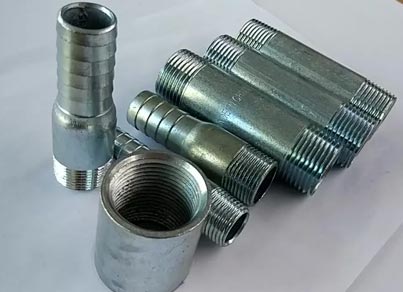
Reducing Nipple
Forged fitting reducing nipples are essential components in piping systems, designed to connect pipes of different diameters. Made from high-quality forged steel, these nipples provide exceptional strength and durability, making them suitable for high-pressure and high-temperature applications.
The reducing nipple allows for a smooth transition between larger and smaller pipe sizes, ensuring efficient flow and minimizing turbulence within the system. Commonly used in industries such as oil and gas, chemical processing, and plumbing, they facilitate flexible piping configurations while maintaining leak-proof connections. The forging process enhances their mechanical properties, ensuring long-lasting performance and reliability in critical applications.
Specification | Details |
---|---|
Material Grades | ASTM A105, A350 LF2, A182 F1, F5, F9, F11, F22, F304, F316 |
Standards | ASME B16.11, MSS-SP-79, ASTM A234 |
Sizes | 1/2" to 4" (DN 15 to DN 100) or custom sizes depending on requirements |
Types | Reducing Nipple (various size combinations) |
Pressure Ratings | Class 3000, Class 6000, Class 9000 |
Connection Type | Threaded or Socket Weld |
Corrosion Resistance | Moderate to High (depends on material grade; may require protective coatings for enhanced resistance) |
Surface Finish | Black, Galvanized, or as specified by customer |
Testing & Certification | Hydrostatic Testing, Positive Material Identification (PMI), Mill Certificates |
Applications | Oil & Gas, Chemical Processing, Power Generation, Water Treatment, and Construction |