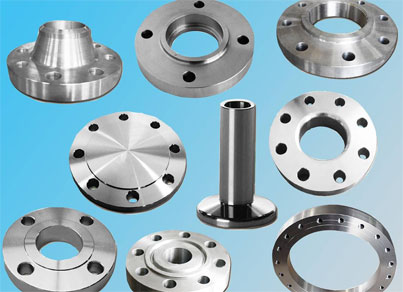
Stainless Steel Flanges
Stainless steel Flanges are widely used in both domestic and industrial applications because of the various benefits it offers. It is resistant to corrosion and temperature and appearance is good. The flanges made of stainless steel offers all these benefits and many more.
Stainless steel flanges are important in industries like transport, gas, water, food, beverage, chemical process etc where piping is required these flanges are used for connections. Flanges are important part of the piping connection and also provides easy access for cleaning, inspection or modification.
Standard | ASTM A182 |
Type | Weldneck, Slipon, Blind, Socketweld |
Grade | 304, 304L, 304H, 310, 310S, 316, 316L, 316ti, 317, 317L, 321, 347, 904L |
Size | 0.5” to 24” |
Class | 150#, 300#, 600#, 900#, 1500# |
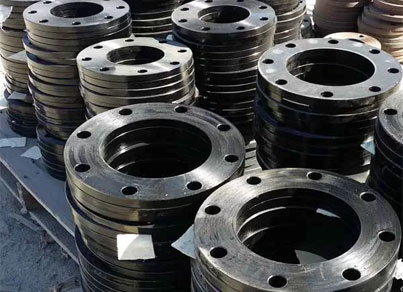
Carbon Steel Flanges
Carbon Steel Flanges are pipe connectors that join two pieces of piping together. They are made using carbon steel material and contain a raised lip or rim that ensures a strong bond is formed between the pipes by welding them together.
Furthermore, they are designed to support greater pressure due to their stronger construction. These metallic connections also provide moderate corrosion resistance, making them ideal for industrial & general purpose applications.
Standard | ASTM A105 |
Type | Weldneck, Slipon, Blind, Socketweld |
Size | 0.5” to 24” |
Class | 150#, 300#, 600#, 900#, 1500# |
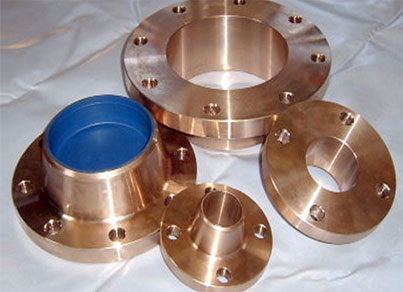
Copper Flanges
Copper flanges play a vital role in various industrial applications due to the unique properties of copper, such as excellent thermal and electrical conductivity, corrosion resistance, and antimicrobial properties.
These flanges are commonly used in plumbing systems, HVAC (heating, ventilation, and air conditioning) systems, and electrical installations. Below is an overview of copper flanges, including their specifications, characteristics, and applications. Copper Alloys: Copper alloys, such as brass (copper-zinc alloy) and bronze (copper-tin alloy), are often used in flange manufacturing to enhance specific properties like strength, corrosion resistance, and machinability.
Specification | Details |
---|---|
Material | Copper, Copper Alloys (Brass, Bronze) |
Standards | ASTM B16.5, ASTM B62, ASTM B584, ASME B16.24, ASME B16.5, DIN 86029 |
Sizes | 1/2" to 48" (Nominal Pipe Size) |
Pressure Ratings | 150#, 300#, 400#, 600#, 900#, 1500# |
Types of Flanges | Weld Neck, Slip-On, Blind, Socket Weld, Threaded |
Temperature Range | Up to 250°C (varies depending on specific copper alloy) |
Corrosion Resistance | Excellent resistance to corrosion in atmospheric and aqueous environments |
Applications | Plumbing Systems, HVAC Systems, Electrical Installations, Industrial Equipment, Marine |
Manufacturing Process | Forged, Machined, Cast |
Testing and Quality Control | Visual Inspection, Dimensional Inspection, Chemical Analysis, Pressure Testing |
Surface Finish | Smooth, Polished, as per customer requirement |
Certification | Mill Test Certificate (MTC) according to EN 10204 3.1/3.2 |
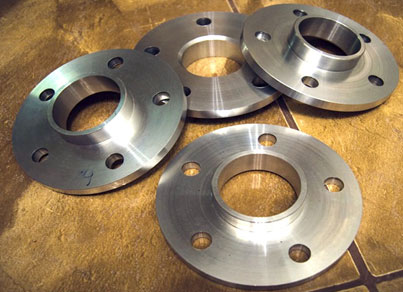
Nickel Alloy Flanges
Scope of Alloy Pipe Impex nickel flanges are perfect for application in various industry for high weight and temperature applications. These flanges are composed with exactness for simple establishment. Aside from standard flanges, we likewise offer hand crafted nickel flanges to meet the particular application prerequisites of the clients.
Item Code: 7219 Port Of Dispatch: Any Production Capacity: Ready Stock Packaging Details: As Per Customer Requirment.
Material Standard | ANSI B16.5, ASTM A182, ASTM A351, ASTM A105 |
---|---|
Product Type | Bars, Pellets, Rods |
Grades | Nickel 200 , Nickel 201 |
Material Grade | All standard grades |
Diameter | All standard sizes |
Material | Nickel Alloy |
Size | >30 inch |
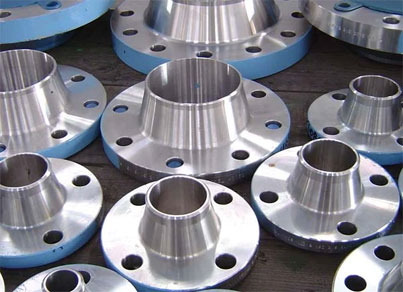
Hastelloy Flanges
Hastelloy is a high-performance nickel-molybdenum-chromium superalloy known for its exceptional resistance to corrosion, especially in harsh chemical environments. Hastelloy flanges are critical components in industries that demand materials capable of withstanding extreme conditions, including high temperatures and corrosive substances.
Hastelloy C-276: Excellent resistance to pitting, stress-corrosion cracking, and oxidizing atmospheres up to 1900°F (1038°C). Commonly used in chemical processing, pollution control, and waste treatment. Hastelloy C-22: Superior resistance to corrosion, especially in oxidizing environments. Widely used in pharmaceutical, food processing, and petrochemical industries.
Specification | Details |
---|---|
Material Grades | Hastelloy C-276, Hastelloy C-22, Hastelloy B-2 |
Standards | ASME B16.5, ASME B16.47, ASTM B564, ASTM B472, DIN 2632, DIN 2633 |
Sizes | 1/2" to 48" (Nominal Pipe Size) |
Pressure Ratings | 150#, 300#, 400#, 600#, 900#, 1500#, 2500# |
Types of Flanges | Weld Neck, Slip-On, Blind, Socket Weld, Lap Joint, Threaded, Orifice, Long Weld Neck |
Temperature Range | -200°C to 1250°C |
Corrosion Resistance | Excellent in various aggressive environments including oxidizing and reducing conditions |
Applications | Chemical Processing, Pharmaceuticals, Power Generation, Marine, Oil & Gas |
Mechanical Properties | Yield Strength: 35-70 ksi, Tensile Strength: 100-150 ksi |
Chemical Composition | Varies by grade; common elements include Nickel (57-70%), Chromium (14-22%), Molybdenum (up to 30%) |
Manufacturing Process | Forged, Heat-treated, Machined |
Testing and Quality Control | Hydrostatic Testing, Ultrasonic Testing, Radiography, Magnetic Particle Inspection |
Surface Finish | Smooth, Rust-proof Oil, Black, Galvanized, as per customer requirement |
Certification | Mill Test Certificate (MTC) according to EN 10204 3.1/3.2 |
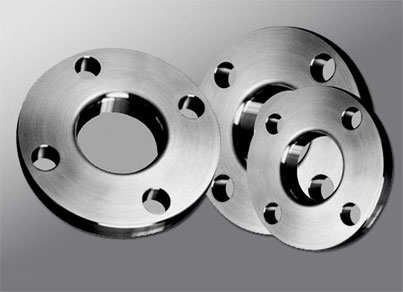
Alloy Steel Flanges
Alloy steel flanges offer high tensile and yield strength, making them suitable for high-pressure applications. Durability: Excellent resistance to wear and tear, providing long service life even in harsh conditions. Temperature Resistance: Capable of withstanding high temperatures without losing strength or integrity.
A182 F1: Contains molybdenum for increased strength and corrosion resistance. Used in high-temperature service applications. A182 F5: Contains chromium and molybdenum, offering good resistance to oxidation and corrosion. Suitable for high-temperature service in oil refineries and power plants. A182 F9: Contains higher chromium and molybdenum content for better corrosion and oxidation resistance. Ideal for high-pressure and high-temperature applications.
Specification | Details |
---|---|
Material Grades | A182 F1, A182 F5, A182 F9, A182 F11, A182 F22 |
Standards | ASME B16.5, ASME B16.47, ASTM A182, ASTM A105, DIN 2632, DIN 2633 |
Sizes | 1/2" to 48" (Nominal Pipe Size) |
Pressure Ratings | 150#, 300#, 400#, 600#, 900#, 1500#, 2500# |
Types of Flanges | Weld Neck, Slip-On, Blind, Socket Weld, Lap Joint, Threaded, Orifice, Long Weld Neck |
Temperature Range | -29°C to 593°C (can vary depending on specific grade and application) |
Corrosion Resistance | Enhanced resistance to oxidation, sulfidation, and other forms of corrosion |
Applications | Power Generation, Petrochemical, Oil and Gas, Chemical Processing |
Mechanical Properties | Yield Strength: 30-80 ksi, Tensile Strength: 60-100 ksi |
Chemical Composition | Chromium (1-9%), Molybdenum (0.5-1%), Nickel, Vanadium, Carbon, Manganese, Silicon |
Manufacturing Process | Forged, Heat-treated, Machined |
Testing and Quality Control | Hydrostatic Testing, Ultrasonic Testing, Radiography, Magnetic Particle Inspection |
Surface Finish | Smooth, Rust-proof Oil, Black, Galvanized, as per customer requirement |
Certification | Mill Test Certificate (MTC) according to EN 10204 3.1/3.2 |